Pneumatic lined ceramic ball valve is an industrial valve characterized by a spherical body coated with ceramic material internally to increase wear resistance, corrosion resistance, and sealing performance. The internal valve core components of ceramic ball valves are made of toughened alumina or oxidized ceramic, which has extremely high chemical stability and hardness (Rockwell hardness HRC88), second only to diamond, and has extremely high wear resistance, corrosion resistance, and erosion resistance. It also has good thermal insulation, low coefficient of thermal expansion, high hardness, and high electrical and thermal insulation, and its performance is superior to other materials. Widely used in harsh working conditions where it is difficult to use metals or other materials, such as chemical equipment, waste incineration equipment, flue gas desulfurization equipment, etc., covering industrial fields such as power, petroleum, chemical, metallurgy, mining, and sewage treatment. The ball is manufactured using advanced grinding equipment and processes, with high roundness accuracy and good surface quality. After being aligned with the valve seat, it utilizes the self-lubricating properties of Zr02 structural ceramics to have excellent sealing performance, completely changing the disadvantages of metal hard sealed ball valves such as easy leakage, high torque, and non corrosion resistance of the sealing surface.
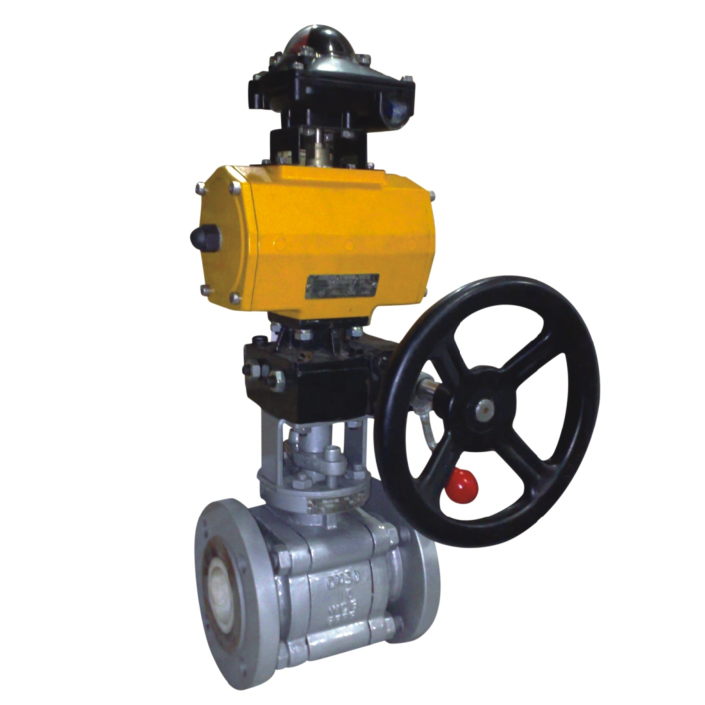
The ceramic ball valve adopts high-tech new ceramic structural materials to make the sealing parts and vulnerable components of the valve, which improves the wear resistance, corrosion resistance, and sealing performance of the valve product, greatly extending the service life of the valve, which is 2-4 times that of alloy and Monel valves. The use of ceramic valves can greatly reduce the number of valve repairs and replacements, improve the safety and stability of supporting equipment operating systems, and save equipment repair costs. This valve is suitable for opening and closing on high hardness granular media or media pipelines with soft particles but corrosive properties. The nominal pressure is PN10~PN40, suitable for a temperature of 200C. It can be manufactured according to standard data such as GBJIS and API.
-Main valve body: usually made of metal material, with inlet and outlet to accommodate fluid channels- Sphere: The sphere is the core component of the valve, usually made of metal material and coated with ceramic material inside. Ceramic layers are used to increase the wear resistance, corrosion resistance, and sealing performance of valves- Drive device: This type of ball valve is usually controlled by a pneumatic (air or gas) drive device to rotate the ball to change the connection of the fluid channel- Sealing device: usually includes a sealing ring and a sealing seat to ensure that the valve does not leak when closed- Control system: The control system can be a pneumatic control system used to set and monitor the operation of valves. Working principle: The working principle of the pneumatic lined ceramic ball valve is similar to that of a regular ball valve. By using a pneumatic drive device and rotating the sphere, fluid connection or separation between different channels can be achieved, thereby changing the flow direction or flow rate of the fluid. The function of ceramic lining is to increase the wear resistance and corrosion resistance of valves, especially suitable for applications dealing with corrosive media. Features and advantages: - Wear resistance: Ceramic lined spheres have excellent wear resistance and are suitable for handling media with high particle content- Corrosion resistance: Ceramic materials resist the erosion of corrosive media, making them highly suitable for chemical and corrosive media treatment- High sealing performance: Ceramic spheres provide excellent sealing performance, reducing the risk of leakage- Remote operation: Equipped with a pneumatic drive device, this ball valve can be remotely operated, reducing the risk for operators- Programmable: Pneumatic control systems allow users to program the opening and closing time and flow direction of valves to adapt to different process requirements- Long life and reliability: Ceramic lined ball valves have long life and reliability, especially suitable for applications that require stable operation. Application areas: This type of ball valve is typically used in industrial applications that require high wear and corrosion resistance, such as mining and metallurgy, for treating abrasive media such as ores, tailings, and wastewater- Chemical industry: used for processing chemicals with high levels of corrosive media and particulate matter- Electric power industry: used to control coal powder, ash and waste gas emissions- Petroleum and natural gas industry: Processing fluids containing solid particles, such as petroleum and oil well wastewater. In summary, the pneumatic lined ceramic ball valve is a valve that performs well in highly corrosive and high particulate matter content industrial applications, with wear resistance, corrosion resistance, and high sealing performance, ensuring the reliability and durability of fluid control.