In many cases, the paint and coating selection for valves is only a temporary coating on new valves, aimed at delaying external corrosion during valve storage or before the final paint or coating of the entire pipeline system after installation.
Except for the black valves in the water treatment plant, the valve standards are almost silent on the paint and coating of new valves, referring to paint as the "manufacturer's standard". The updated version of the American Petroleum Institute (API) 600 adds that the paint should be silver or aluminum. For many years, an API 600 valve manufacturer has painted its black valves in a pleasant light blue color.
Blue valve
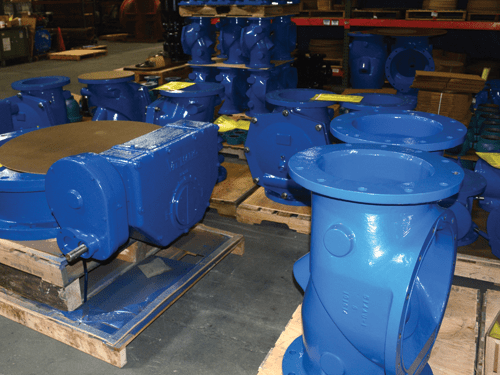
Although OEM paint may be basic for valve manufacturers, today's end-users have detailed paint and coating requirements for many valves they purchase. These requirements go far beyond the simple silver or black coating that wraps the valve when it leaves the factory.
But what are the paints and coatings used?
Most of us know that paint is usually related to diluents. This diluent indicates that the paint or coating contains more than one compound or chemical component. Most of them are organic compounds composed of carbon based components. They contain four main elements:
Pigments not only provide coloring, but also contribute to the corrosion resistance and overall strength of coatings or paint mixtures
Additives, including thickeners, UV stabilizers, and defoamers
Resin, composed of acrylic and epoxy resins, can combine all components to form a uniform substance
Solvents that affect the drying time and viscosity of coating mixtures
The most basic industrial coatings for valve paint and coating selection are clear varnish and enamel. These polymer types constitute the common vanilla in the industrial coating industry. For residential and commercial applications, water-based acrylic resin is preferred. In some countries with very strict regulations on volatile organic compounds (VOC), water-borne acrylic lotion (referred to as lotion coating) is used for industrial applications.
Specific coatings have dozens of different components. Each end user may have many different requirements, depending on specific weather exposure and factory environmental impacts. All these different coatings have two requirements: first, appropriate surface treatment, and second, the need for primer.
Primer is the interface between the final paint or coating and the substrate. They provide temporary corrosion resistance during transportation and storage. The most popular type of industrial primer is anti-corrosion zinc based paint.
surface treatment
Appropriate surface treatment is essential for the successful application of any coating. The surface can be prepared chemically or mechanically. The chemical preparation process produces an etched surface, providing greater biting force for the coating to be applied. Mechanical surface treatment involves removing surface defects through water or dry spraying techniques. In rare cases, old-fashioned polishing or brushing methods are still used. Different paints require different surface treatments to adhere correctly.
Before applying any coating, grease, oil, dirt, and rust will be removed.
The SSPC document specifies detailed surface treatment procedures and requirements. SSPC has also issued a series of standards and recommendations for all types of industrial coatings and paints.
SSPC and NACE International (NACE) have varying degrees of coating and coating surface treatment specifications (Table 1).
The two most commonly cited surface treatment methods are SSPC SP6 (commercial sandblasting cleaning) and SP10 (near white sandblasting cleaning).
Excessive preparation
Due to improper protection during coating surface treatment, thousands of valves and actuators are damaged every year. Linear valves seem to suffer the most damage, especially external thread and yoke (OS&Y) valve cover valves. The right angle rotary valve cannot be protected from damage during the surface treatment stage. Some areas that are frequently damaged during surface treatment sandblasting include the areas listed in Table 2.
Coating type:
Acrylic fiber. Acrylic coatings used for protective coatings are based on organic or water-based solvents. Waterborne acrylic lotion coating is also called lotion coating. They are usually used when there are VOC release issues during the coating process.
Alkyd resin. Alkyd resin is a type of polyester resin modified with fatty acids. Due to the chemical reaction between fatty acids and air, most alkyd coatings will dry out.
Epoxy resin. Epoxy resin coating is a resin composed of two parts. When they combine, a chemical reaction occurs between the epoxy resin and the curing agent, causing the epoxy resin to cure. Epoxy resin is usually a very tough and corrosion-resistant coating, but their service life is very short. The UV stability of most epoxy resin coatings is also poor.
Polyurethane. Like most epoxy resins, polyurethane is a two-part coating. They have a smooth surface and are commonly used as the final coating for epoxy resin and zinc primer.
Correct coating
The first question that needs to be answered when choosing a coating is "Why should equipment be coated?" In pipeline systems and valves, the answer is usually corrosion resistance rather than overall attractiveness.
The second and most important issue involves the environment in which the coating is exposed, such as:
Is there any chemical smoke nearby?
What is the working temperature?
Is there a possibility of chemical splashing or spillage?
Will the coating cover the insulation material?
Will the coating be cleaned? What cleaning techniques and chemicals will be used during the cleaning process?
Will the coating be applied to existing coatings?
Other questions regarding the correct selection include: where the coating will be applied, in the workshop or on-site; What is the expected service life of the coating?
The last question is: What is the budget for the paint? This question often surpasses other questions, depending on budget, expected lifespan, and other considerations.
Examples from the real world
The painting specification consists of three parts, forming a complete painting process. They are: 1) pretreatment and surface treatment, 2) application of paint or coating, and 3) curing of paint or coating. Paint or coating is converted into a solid film through the curing process. This curing can be carried out at room temperature or in an oven.
The paint or coating requirements of the end user are different from those of the valve manufacturer. Here are some example paint/coating specifications for these two entities:
Petrochemical plants, general pipeline systems, including ball valves, butterfly valves, and gate valves:
Surface treatment: SP10
First layer: Phenolic epoxy resin
Second layer: Phenolic epoxy resin
Offshore facilities, process equipment, and pipelines:
Surface treatment: SP5
First coating: solvent inorganic zinc
Second layer: Silicone Acrylic
Ball valve manufacturer, standard surface treatment:
Surface treatment: SP3 (equivalent)
First coat of paint: Phenolic modified alkyd resin paint
Second layer: Synthetic resin aluminum paint
Manufacturers of gate valves, globe valves, and check valves:
Surface treatment: SP6 or SP3
Bottom coat: Phosphate
First coat: Modified alkyd resin primer
Second coat of paint: Organic silicon modified alkyd resin paint
Compact doors, globes, and inspection valves designed according to API 602 are typically unpainted in the factory. However, they typically have corrosion-resistant (such as phosphate) coatings to prevent corrosion until they are installed and the pipeline system obtains its final coating.
The development of dozens of paint and coating options helps extend the service life of installed valves. This means that potential leaks caused by external corrosion have been almost eliminated. In addition, with continued attention to unorganized emissions, reducing leakage issues is certainly a good thing.