Manual pneumatic dual-purpose flange ball valve is a commonly used control valve that combines the functions of manual and pneumatic operation. It usually consists of the following parts:
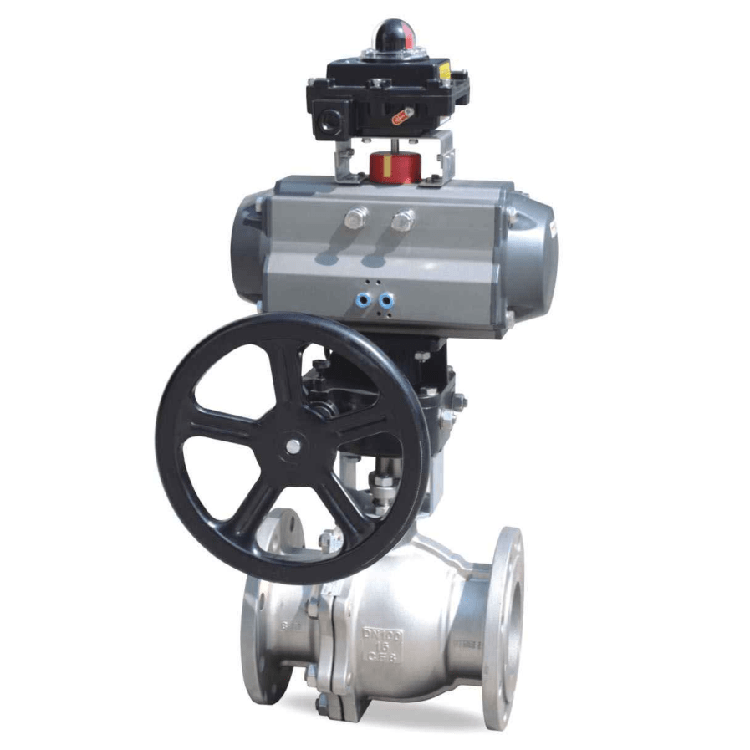
Flange connection: Ball valves typically have flange connections for connection to piping systems. Flanges typically use standard dimensions and standardized connection methods, such as ANSI, DIN, or JIS.
Valve body: The valve body is the main part of a ball valve and is usually made of metal materials such as cast iron, stainless steel, or copper alloy. There is a spherical hole inside the valve body, which controls the flow of the medium by rotating the sphere.
Sphere: A sphere is a key component of a ball valve, typically made of metal and having a spherical bore. The rotation of the sphere determines the continuity of the fluid. When the sphere rotates to align with the pipeline, the fluid can pass through; When the sphere rotates to make the pore perpendicular to the pipeline, the fluid is intercepted. Valve stem: The valve stem is connected to a manual operating device and a ball, and is used to rotate the ball during manual operation. The valve stem usually has a handwheel or handle for manually controlling the opening and closing of the ball valve.
Operating device: The manual and pneumatic dual-purpose flange ball valve has two operating modes: manual and pneumatic. Manual operation is usually carried out through a handwheel or handle, while pneumatic operation is achieved through pneumatic actuators. Pneumatic actuators can receive compressed air or other gas signals and convert them into force or torque, thereby achieving automatic opening and closing of ball valves.
Sealing structure: Ball valves have good sealing performance to ensure the normal operation of fluids and prevent leakage. Reliable sealing materials such as PTFE (polytetrafluoroethylene) or metal sealing rings are usually used.
The advantage of a manual pneumatic dual-purpose flange ball valve is that it combines the functions of manual and pneumatic operation. Manual operation is suitable for small flow rates or situations that require temporary control, while pneumatic operation is suitable for large flow rates, remote control, or automation systems. This design provides greater flexibility and operational convenience, suitable for various industrial applications such as chemical, petroleum, pharmaceutical, power, etc.