It consists of a 3810 series (PSL series) electric actuator and a small flow regulating valve body. The actuator contains feeding function and accepts a unified 4-20mA or 1-5V · DC standard signal. It converts the current signal into a corresponding linear displacement, automatically controls the opening, and achieves continuous adjustment of process parameters such as pressure, flow rate, temperature, and liquid level of the fluid in the pipeline. It is a small-diameter regulating valve specifically developed for small flow regulation. It has the characteristics of small size, light weight, high performance, and precise control for small flow rates. When the electric small flow regulating valve cannot regulate the clean medium, attention should be paid to the problem of small throttling clearance and the prevention of blockage. Suitable for regulating the main flow of liquid, steam and other media.
1. Main technical parameters of electric small flow regulating valve
Valve body form
Straight through casting and forging valve body
Nominal diameter
DN15~25mm
Valve seat diameter
Dn3~25mm
Nominal pressure
PN 1.6、2.5、4.0、6.4、10.0、16.0 MPa
Connection form
Welding (SW BW), threading (applicable to flanges within 1 inch)
Valve cover form
Standard Type -17~+250 ℃, High Temperature Type+250~+450 ℃, Low Temperature Type -60~-196 ℃, Bellows Sealed Type -40~+350 ℃
Cover type
Bolt compression type
Sealing packing
V-shaped PTFE packing, PTFE impregnated asbestos packing, asbestos textile packing, graphite packing
body material
38136;; 38050; WCB, not 38152; 38050; CF8, CF8M, CF3, CF3M)
2. Valve internals
Valve core form
Single seat plunger type valve core
Traffic characteristics
Linear, equal percentage
Valve core material
Stainless steel (304, 304L, 316, 316L)
3. Actuator
Model of actuator
3810L series, PSL series and imported actuators
Main technical parameters
Power supply voltage: 220V/50Hz, input signal: 4-20mA or 1-5V · DC, output signal: 4-20mA · DC
Protection level: IP55, explosion-proof mark: Exd Ⅱ BT4, manual operation function: handle
Environmental temperature: -25~+70 ℃, environmental humidity: 95%
3、 Performance indicators
project
Indicator value
Basic error%
Equipped with 3810L2.0; Equipped with PSL1.0
Return difference%
Equipped with 381L 2.0; Equipped with PSL1.0
Dead zone%
one
Constant point deviation%
Electric opening
Starting point 2.5
Endpoint 2.5
Starting point 2.5
Endpoint 2.5
Electricity off
Starting point
two point five
End
two point five
Rated travel deviation%
two point five
Leakage rate L/h
0.01% rated capacity of valve
Adjustable range R
50:1
4、 Rated flow coefficient Kv, allowable pressure difference
Nominal diameter DN
G3/8"、 1/2"、 G3/4"、 G1'
Valve seat diameter dN
three
four
five
six
seven
eight
nine
ten
eleven
twelve
Rated flow coefficient KV
zero point zero eight
zero point one two
zero point two zero
zero point three two
zero point five zero
zero point eight zero
one
one point four zero
one point five five
one point eight five
Rated travel
ten
ten
ten
Allowable pressure difference (MPa)
Nominal pressure
5、 Main technical data
1. Main technical performance indicators
project
index
Leakage rate
Single seat: metal valve seat: Class IV, 10-4 below rated flow; soft valve seat: Class VI, 10-7 below rated flow
Sleeve: Single sealed type IV grade, less than 10-4 of rated flow; Double sealed type III, less than 10-3 of rated flow.
Compliant with GB4213-92 standard
Basic error
2.5%
Return difference
2%
Dead zone
3%
Always point deviation
2.5%
Rated travel deviation
2.5%
6、 Installation size
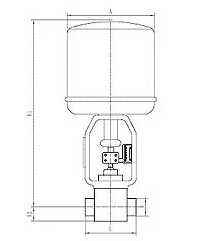
Valve diameter
L
Equipped with electric power
H1
H2
A
3/8”
DN10
eighty
five hundred and twenty
twenty-six
two hundred and thirty
1/2”
DN15
eighty
five hundred and twenty
twenty-six
two hundred and thirty
3/4”
DN20
ninety-two
five hundred and eighty
thirty
two hundred and thirty
1”
DN25
one hundred and eleven
five hundred and eighty
thirty
two hundred and thirty
Due to product improvements, technological innovations, or special requirements, the connection dimensions of various valves may change. Please contact our technical department for the latest product information. We can also customize valves with special structural dimensions according to your on-site requirements. The flange welding groove and other size connections of the valve shall comply with the relevant requirements of various standards.
Seven methods for use, maintenance, and troubleshooting
1. Installation and use
Failure to install regulating valves that do not meet requirements can result in significant waste. Conversely, proper installation can ensure normal operation and extend their service life. Reduce maintenance workload and achieve good system control performance.
(1) The installation of regulating valves should generally consider the following aspects:
① Safety: The safety of personnel and equipment during the installation process.
② Control performance: The pressure loss of the piping system should be consistent with the pressure loss considered when calculating the size of the regulating valve to ensure the required flow characteristics. Import and export should strive to ensure sufficient straight pipe sections.
③ Installation location: There should be sufficient space for manual operation by operators (including bypass operation) and the possibility of on-site disassembly and maintenance of regulating valves and accessories.
④ Regulating valve group: Generally, bypass valves with shut-off valves are installed in the process piping to form a valve group with regulating valves, in order to meet the needs of continuous operation of equipment. Use a shut-off valve to isolate the regulating valve during maintenance. Adjust with a bypass valve. The recommended arrangement of the regulating valve group in the following figure.
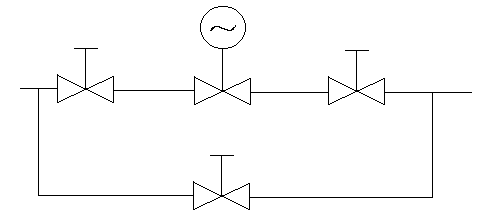
Installation legend of bypass pipeline
(2) On site installation
The installation personnel should first recognize that the regulating valve is a precision instrument and equipment, and should not collide or fall to avoid damage. Please pay specific attention to the following points:
① It is best to install the valve upright and vertically on the pipeline. In situations where the valve has a large self weight and there is vibration, a support frame should be added.
② The valve body should avoid being subjected to excessive stress due to significant differences in axis between the front and rear piping or the flanges being adjusted.
③ Before the initial start of work and after shutdown maintenance, the piping system should be flushed first before installing the regulating valve. Or install a transition filter in front of the valve.
④ The regulating valve must be installed according to the arrow indicating the flow direction on the valve body.
2. Fault analysis and troubleshooting
Common fault states
Cause of malfunction
Exclusion method
The motor does not operate
No power input
Disconnected or disconnected wires
Different and low power supply voltages
The capacitor is broken down
Different input signals
Thermal protection action. (High ambient temperature, high frequency of use)
turn on electricity
Replace the wires or connect the wires correctly
Check the voltage with instruments
Replace the power capacitor
Change input signal selection
Reduce the surrounding temperature, lower the frequency of use or sensitivity
Valve does not operate
The valve core and liner or valve seat are stuck
Valve core detachment, valve stem bending or breaking
Disassemble and reassemble
Replace the valve stem or pin
Manual operation is laborious
The packing gland is too tight
Abnormalities occur inside the valve
Loosen the pressure cover
Disassemble the valve for inspection
Stop during automatic adjustment process
Overloaded starting under excessive load
Thermal protection action
Foreign objects enter the valve body
The packing gland is too tight
Check the regulating valve to eliminate the load
Check the regulating valve to eliminate the load
Disassemble the valve
Loosen the pressure cover
Do not send an opening signal
Poor contact or disconnection of the opening signal wiring
Check the connection of the opening signal wiring
The opening signal cannot reach full closure
Poor installation of potentiometer
Check the installation of the potentiometer
The motor does not stop rotating when reaching the limit position
Poor adjustment of limit switch limit position
Poor installation of limit switch
Readjust
Reinstall
Common fault states
Cause of malfunction
Exclusion method
Adjustment sensitivity decreases, motor torque decreases
Insufficient voltage of the motor, low or different voltage of the power supply
Check the voltage with instruments
The regulating valve oscillates at any opening
Unstable support
There is a vibration source nearby
Wear of valve core and bushing
Strengthening support
Take measures to reduce and eliminate vibration
Adjust and eliminate wear gaps
Slow action of regulating valve
Blockage or coking caused by mud or highly viscous media inside the valve body
Sealing PTFE packing has hardened and deteriorated
Wash the inner cavity of the valve body
Replace the packing material
The valve leaks significantly when fully closed
The valve core or seat is corroded or worn
The thread on the outer circle of the valve seat is corroded
Replace the parts
Replace the parts
Leakage at packing and connection points
The cover is not tightly pressed
Aging and deterioration of PTFE filler
Valve stem damage
Tighten the hexagonal nut and loosen it
Damaged sealing gasket
Tighten the connecting bolts
Replace the packing material
Replace the valve stem
Re tighten the connecting bolts
Replace the sealing gasket
3. Maintenance and Repair
(1) Maintenance
① Regularly inspect the pipeline for rust, welding slag, dirt, and dust.
② Regularly check the support frame for heavy weight and vibration situations.
③ The power supply must not have any malfunctions.
④ The sealing gasket at the connection between the valve body and the upper valve cover has been used for a long time and should be replaced in a timely manner. To replace it, simply remove the upper valve cover and place a new sealing gasket.
⑤ If there is leakage in the packing box, the sealing packing should be replaced in a timely manner. When replacing, the valve stem should be disconnected, the pressure plate and packing cover should be removed, and new packing can be installed.
⑥ Regular maintenance.
⑦ When parked for a long time, protective covers for connecting flanges should be installed, so all interfaces should be plugged with plastic plugs. When parking, ensure the overall verticality or horizontal position of the valve,
⑧ Do not support the valve in sensitive areas such as valve positioners, fittings, wiring, etc.
(2) Repair
When the regulating valve cannot meet the operating requirements during use, or undergoes regular inspections to prevent accidents after a long period of operation, it must be carefully repaired. The maintenance work usually includes the following main contents:
① Valve cleaning - When repairing a valve removed from a process pipeline, all components that have been immersed in the process medium must be cleaned thoroughly. To prevent damage to personnel and equipment caused by corrosive or other harmful fluids. At the same time, the rust on the exposed surface of the components should be removed.
② Valve disassembly - to inspect all components and determine the scope of repair and replacement. Firstly, the actuator and valve should be completely disassembled. When disassembling, it is necessary to protect precision machined parts such as valve cores, valve seats, valve stems, push rods, shaft sleeves, and all precision machined surfaces of the components to prevent damage and minimize maintenance costs. Special tools should be used to disassemble valve seats.
③ Maintenance of main components - if there are small rust spots and wear on the throttling surface of the valve core and the sealing surface of the valve core and valve seat. It can still be repaired using general mechanical processing and grinding methods. If the damage is severe, new parts must be replaced. During repair, it is required to ensure the coaxiality of the valve core and valve seat.
The sealing surface of the valve stem is damaged and can only be replaced with new parts.
Damage to the guiding and sealing surfaces of the push rod. The reaction actuator must be replaced with new parts. And for the positive actuator, appropriate repairs can still be made.
If cracks or other defects affecting the strength are found during the maintenance of the compression spring. Then a new replacement must be used.
④ Replacement of vulnerable parts - The vulnerable parts of this regulating valve mainly include packing, O-ring seals, gaskets, diaphragms, and other components.
During each maintenance, the disassembled packing, O-ring, and gasket must be replaced with new parts. After removing the diaphragm, it is necessary to check for any cracks, aging, and signs of wear that may indicate possible rupture, and then decide whether to replace them based on the specific situation. Generally, it must be replaced within 2-3 years at most.
⑤ Assembly and debugging - During assembly, appropriate lubricating grease should be applied to the positioning, guiding, and threaded connection parts of the components to facilitate disassembly for the next maintenance. Moreover, special attention should be paid to the coaxiality of the push rod, valve core components, and valve seat in the entire machine.
After installation and debugging are completed, the product must pass the factory test items specified in the standard before it can continue to be installed and used.
8、 Transportation and Storage
1. Before storage and transportation, check whether various signs are complete, intact, clear, and whether the packaging boxes are neat and firm, without damage or cracking. Finally, check the reliability and safety of the nail box wrapping.
2. During transportation, it should be loaded and unloaded gently, and throwing, sliding, and impact are strictly prohibited. All types of signs must not be lost, dampened, or damaged.
3. Stored indoors at an air temperature of 5-40 ℃ and a relative temperature not exceeding 90%, the air does not contain harmful impurities that corrode valves.
4. Place according to the markings on the surface of the packaging box and do not invert.
5. The rust prone parts of the product are coated with rust proof grease and wrapped with rust proof paper, with a rust proof period of not less than one year.
6. There should be petroleum asphalt or plastic film inside the packaging box as a rainproof measure.
7. The product packaging has a protection period of one year from the date of leaving the factory.
9、 Unpacking and Inspection
1. After the product is transported to the user, open the packaging box, lift it steadily, handle it carefully, and open the grease paper on the flange hole to install and use it.
2. The packaging box should include the product user manual, product packing list, product qualification certificate, and product quality tracking card.
To meet the requirements of user product completeness, valve positioners, handwheel mechanisms, pressure reducing valves and other accessories can be supplied in sets.
10、 Ordering Notice
1. Product model and name; 2. Nominal diameter DN (mm); 3. Nominal pressure; 4. Traffic characteristics; 5. Valve body material; 6. Rated flow coefficient; 7. Type of medium and temperature range; 8. Pressure difference before and after the valve; 9. Power supply voltage and control signal; 10. Other special requirements.